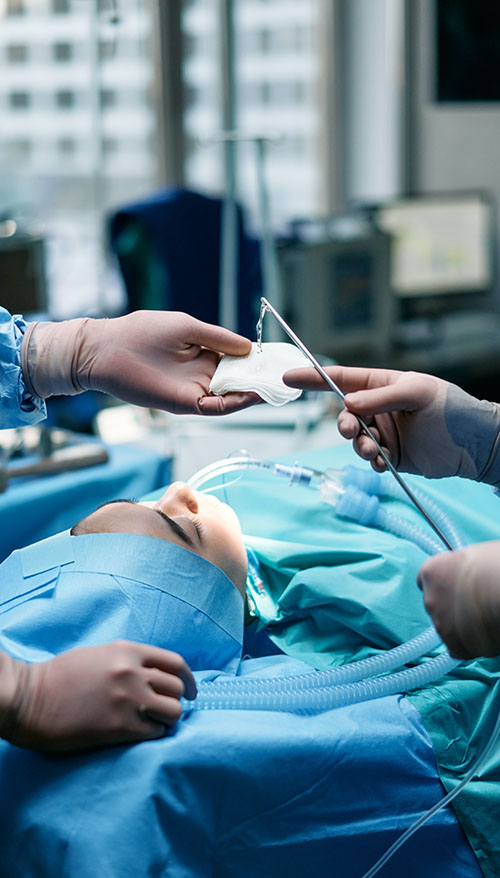
Lubricious, Low Friction Coatings Reduce Tissue Damage During Minimally Invasive Surgery
Harland’s Lubricent® UV Hydrophilic Coatings enable catheters and guidewires to navigate through the most difficult anatomies. Minimally invasive surgery enabled by medical devices with surface enhancements has emerged as the gold-standard for efficient, low-risk surgical procedures. It is a cost effective, and patient-friendly method of performing an operation. Minimally invasive techniques satisfy patients’ desires for a swift recovery and shorten the hospitalization period. The pressures to reduce healthcare costs and improve outcomes are driving minimally invasive medical devices to replace more and more traditional surgical procedures.
Advances in surface enhancements, especially low friction hydrophilic coatings, have accelerated minimally invasive surgery’s growth. These lubricious, low friction coatings now impact a variety of surgical specialties, including cardiovascular, orthopedic, urological, peripheral and neurological procedures.
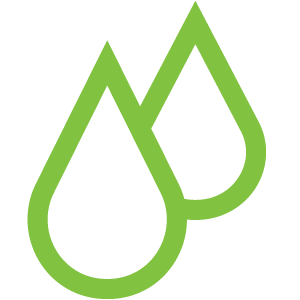
Extreme Lubricity
Lubricent UV Hydrophilic Coating reduces friction forces as much as 98% compared with an uncoated device surface. This enhanced surface performance increases the device’s ability to navigate through tortuous anatomical pathways, improves device control, reduces tissue damage and adds to patient comfort.
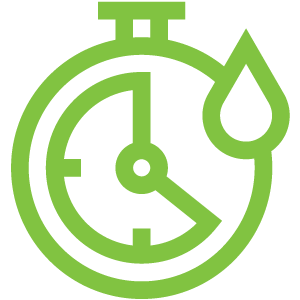
Faster Processing
Because Lubricent UV Hydrophilic Coating cures quickly with UV light, it offers superior processing compared with heat-cured systems. Each coat is generally fully cured in 3 minutes or less, while heat-cured coating systems can require several hours to fully cure. Also unlike heat-cured systems, whose high curing temperatures can degrade a device’s strength and flexibility, Lubricent Coating has minimal impact on the physical properties of the base material.
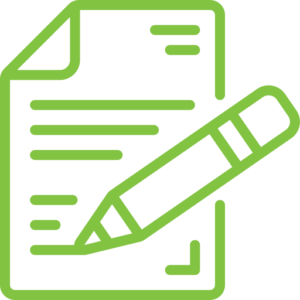
Material Description
Harland’s Lubricent UV Hydrophilic Coating consists of a blend of a hydrogel-forming polymer combined with a proprietary photo-reactive compound dissolved in isopropyl alcohol. When stimulated by a specific spectrum of UV light, the photo-reactive compound crosslinks the polymer into a water trapping hydrogel and binds the coating to the device surface.
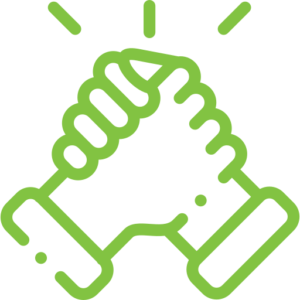
Regulatory Support
Available to supplement and accelerate your FDA and CE Mark submissions. In addition, Harland has experienced regulatory staff to assist you.
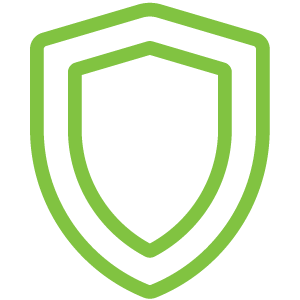
Outstanding Durability
The photochemical covalent bond to the substrate produces superior adhesion and wear resistance while minimizing particulate formation.
Hydrophilic Coating Biocompatibility
Lubricent UV Hydrophilic Coating has been successfully tested by an independent testing facility for ISO10993 biocompatibility. Specific tests included Cytotoxicity, Irritation, Acute Systemic Toxicity, Hemocompatiblity, Allergenic Potential, and Pyrogenicity.
Lubricity and Durability of Harland Hydrophilic Coating on Pebax 75D & Nylon 12 Sample
Pictured on the right are the friction test results from a Lubricent UV Hydrophilic coated sample. Testing was conducted on a Harland FTS Friction Test System. The graph displays the resistance force needed to pull the coated sample between the silicone rubber pads clamped on the sample with 600 grams of clamping force. For comparison, uncoated surfaces typically measure 400 – 600 grams of resistance force and PTFE coated samples exhibit 100 – 150 grams of resistance force.
Back to RESOURCES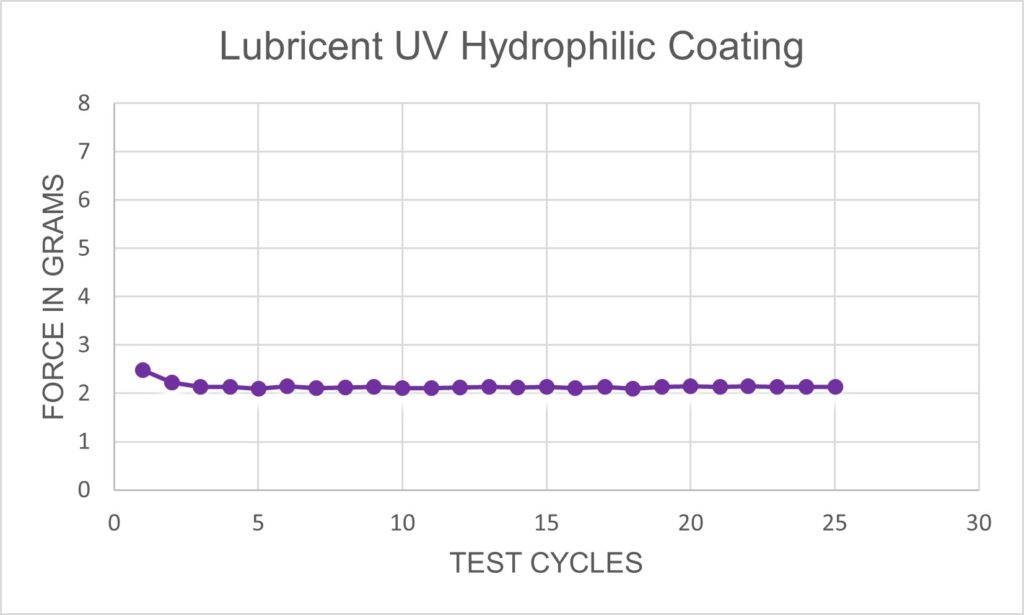