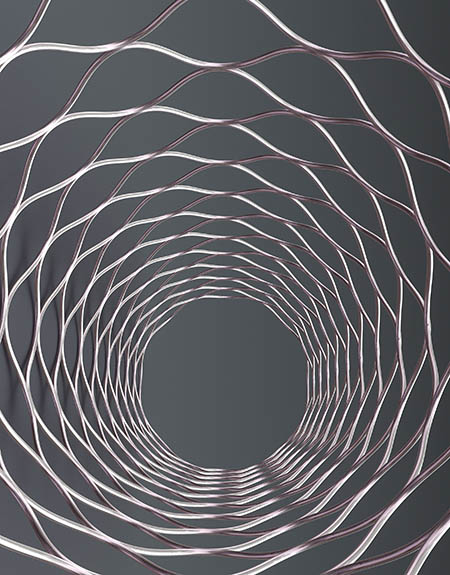
Introduction
Medical device coatings are emerging as the gold standard for efficient, low risk medical procedures. Advances in surface enhancements, especially low friction hydrophilic coatings, have accelerated minimally invasive surgery’s growth. Lubricious, low-friction coatings positively influence a variety of surgical specialties such as cardiovascular, orthopedic, urological, peripheral and neurological procedures.
Medical OEMs have many choices to make when selecting a coating program for their medical device. With all the options on the market, it is important to find a program that best suits your requirements.
Here are some important factors to consider when selecting a coating program for medical devices such as catheters, guidewires, introducers and other devices:
01
Do you charge royalty and license fees?
In most cases, coating companies charge fees for license agreements and royalty costs. Beware of these costs, they can be hidden and add up to significant costs throughout the program. Before you select the appropriate chemistry and materials, make sure to ask your supplier about license and royalty costs.
02
How efficient is your coating process?
When searching for a coating supplier, seek a company that is dedicated entirely to serving medical device customers, offering a highly efficient coating process. Coating processes can be inefficient and expensive when utilizing companies that lack experience and do not fully understand the technical aspects of the coating process.
03
Does your hydrophilic coating meet the requirements of the device?
The first step in the selection process is to define what type of materials and chemistry are available on the market that will meet your requirements. What performance parameters are crucial to launching your device in the market? Once you define these requirements, you can begin the process of selecting a high quality coating to meet your hydrophilic requirements.
04
Does the coating meet the lubricity requirements for the device?
High lubricity is very important because it provides reduced friction forces compared with an uncoated device surface. This enhanced surface performance increases the device’s ability to navigate through torturous anatomical pathways, improves device control, reduces tissue damage and adds to patient comfort.
05
Has the coating been successfully tested for biocompatibility?
For applications where biocompatibility is required, it is important to make sure the coating has been successfully tested by an independent testing facility for ISO10993 biocompatibility. Specific tests include Cytotoxicity, Irritation, Acute Systemic Toxicity, Hemocompatiblity, Allergenic Potential, and Pyrogenicity.
06
How durable is the coating?
Durability is crucial to the coating surface. The ideal chemistry will provide the photochemical covalent bond to the substrate producing superior adhesion and wear resistance while minimizing particulate formation.
07
Is the coating compatible to the substrate materials of the medical device?
Make sure the hydrophilic coating chemistries are compatible with the substrate materials typically used in the construction of medical devices.
08
What type of techniques are used to apply the coating to the surface?
Hydrophilic coatings can be applied to surfaces in a number of ways. Dip coating is the most common process used to coat medical devices. The dip coating process lowers the devices into a liquid coating solution and then lifts it up at a regulated speed. The coating sticks to the surface and the device is lifted out of the solution.
Spray coating is another technique used to apply the coating. The coating is sprayed onto the surface of the device.
After the coating is applied, the next step is to dry or cure the device. The two major methods for curing hydrophilic coatings are ultraviolet light (UV) and heat. In UV curing systems, the coating is exposed to UV light causing a chemical reaction to dry it.
In a heat cure system, ovens dry the products for a specific amount of time. Controlled heating accelerates drying and any necessary chemical reactions taking place within the coating that allow it to adhere to the surface.
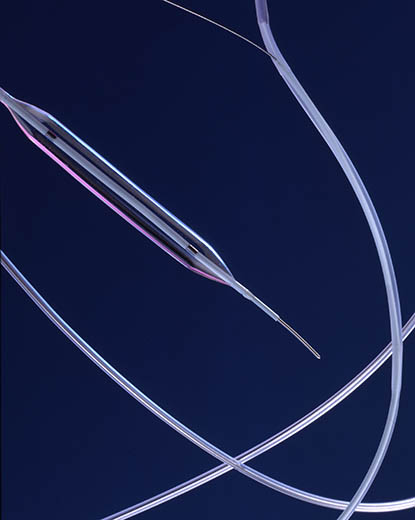
OTHER OPTIONS TO CONSIDER
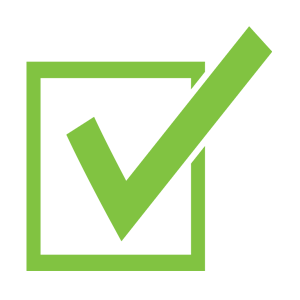
Manual or automated
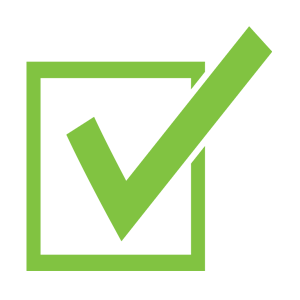
Maximum device length
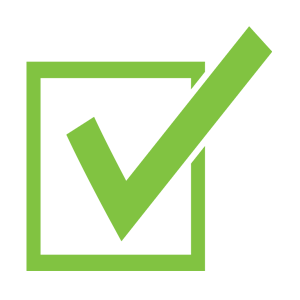
CE Marked
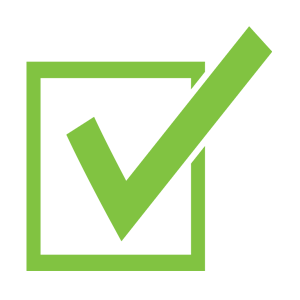
Local language capability
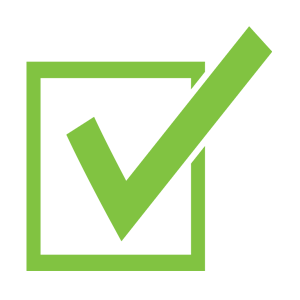
Cleanroom compatible
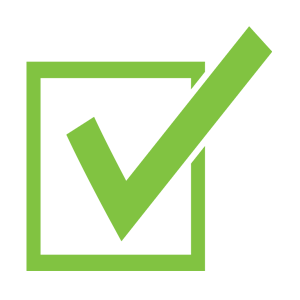
Friction and coating durability testing
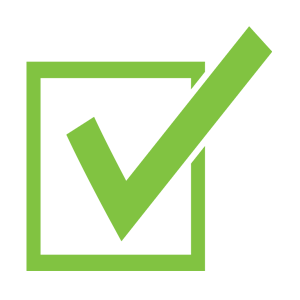
CE Marked
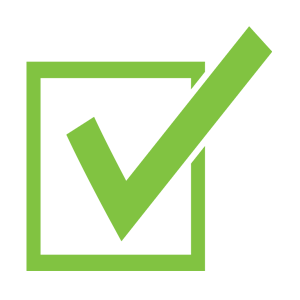
Local Language Capability
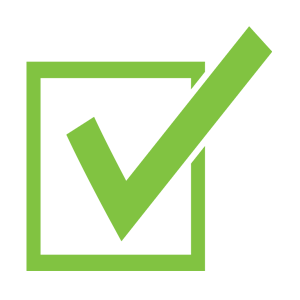
Cleanroom Compatible
10
What type of machine capability do you offer?
There are many automated product platforms on the market designed for coating, testing and processing medical devices. Users have the choice to purchase a UV coating machine for their facility to meet their requirements or selecting a vendor that has the machine experience and capabilities in-house to support the equipment needs.
When selecting one of these automated product platforms, make sure the equipment is designed and manufactured to meet the critical coating, testing, and processing requirements of the medical device. In addition, make sure the company you purchase the machines from has the experience and capabilities to support your needs.
11
What type of coating method development experience do they have?
Coating method development includes processes and protocols that effectively and efficiently apply medical device coating to materials. The application process is just as important as the coating solution in providing optimum medical device coating performance. Before you commit to a full-production coating program, work with your coating vendor to complete a feasibility to prove the coating method is successful and meets your device requirements.
12
What type of coating manufacturing is available?
Once you have completed the method development process, the next step is to determine the coating manufacturing process.
If you are considering outsourcing your coating services, there are significant benefits of having the entire program from a single supplier in one location. Typically, process stability increases because there is less room for error and the quality is easier to manage. Overall, the coating program is much less hassle for the customer.
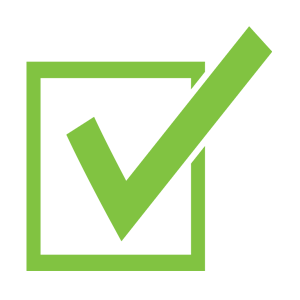
Process stability – less room for error
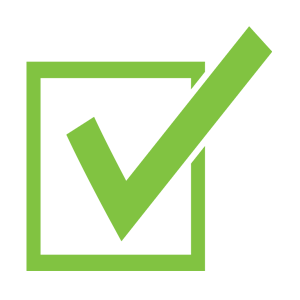
Easier to manage quality
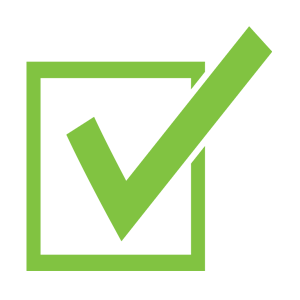
Less hassle for the customer
If you do transfer the coating services to the customer location, make sure consider the following:
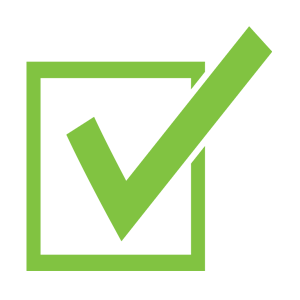
Equipment variables
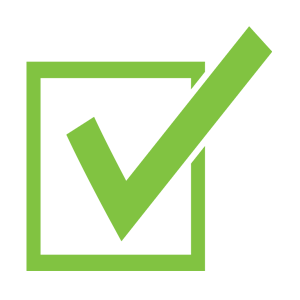
Chemistry management/
understanding process
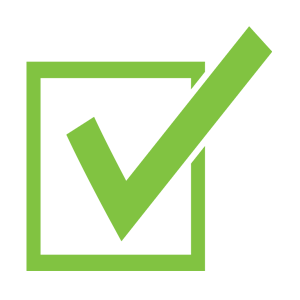
Environment (watch for humidity – can cause tackiness)
13
What type of clean rooms are available for manufacturing?
14
Are they in compliance with the ISO 13485 standards?
15
Do you have full production coating capability?
Make sure the company you work with encourages close customer participation in understanding your coating objectives, developing the exact balance of properties to meet these objectives and validating the process to ensure your coating is fully ready for production, either at your plant or the selected external coating services facilities.
16
What type of regulatory support do you offer?
Find a company with experienced in-house regulatory personnel to advise you for effective and efficient regulatory submissions, including those involving combination drug/devices.